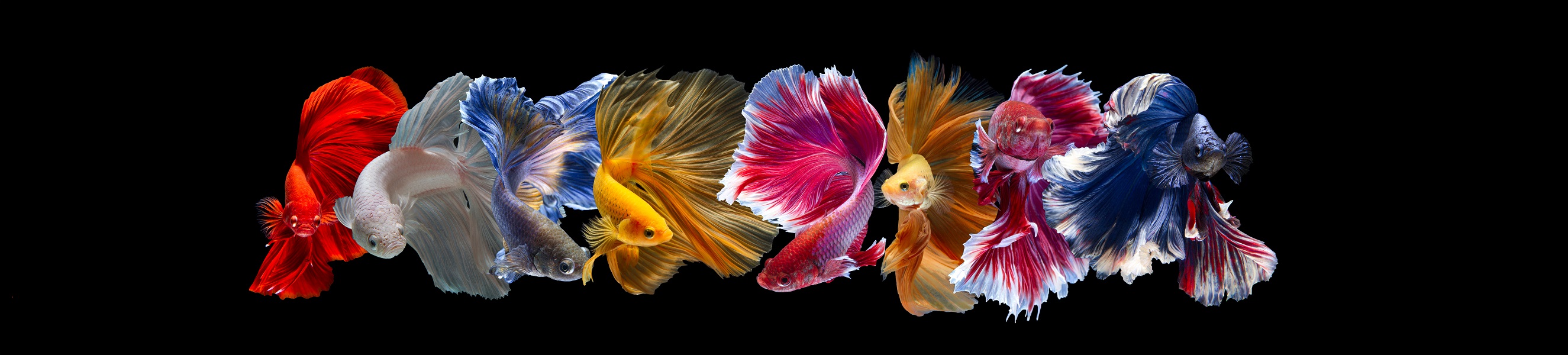
Powder Coating Troubleshooting Guide
1- Unfavorable storage condition (High heat / humid area)
2- Storage has exceeded the shelf life of powder
1-1- Sift the powder using sieve number 200-300 microns
1-2- Check optimal powder storage conditions in technical data sheet
1-3- Store powder at less than 25 °C
2-1- Use a fresh batch of powder
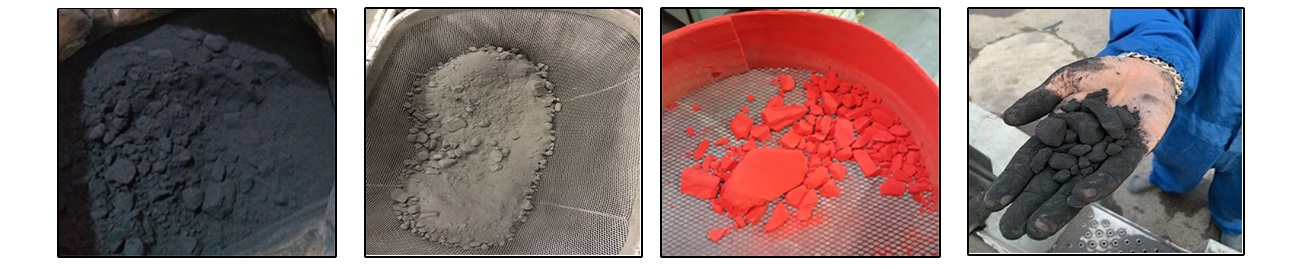
1- Air Pressure is too low or too high
2- Powder settled at the hopper bottom (old powder or poor storage conditions)
3- Oil or moisture in compressed Air
4- Powder is moist or is too fine
5- Air channels of the flow plate are clogged
1-1- Control and adjust the air pressure
1-2- Replace hose or use a hose with larger diameter
1-3- Check air filtration system (filter, pipes and air) and make sure hoses or filters are not clogged
2-1- Stir the powder or sift it using sieve number 200-300 microns
2-2- Check optimal powder storage conditions in technical data sheet
2-3- Store powder at less than 25 °C
2-4- Use a fresh batch of powder
3-1- Check air for oil & moisture (Filters and Moisture Traps in the air system)
4-1- Increase virgin powder or change the powder
4-2- Check optimal powder storage conditions in technical data sheet
5-1- Empty the hopper, clean the pores of the fluidizing plate & if necessary replace the fluidizing plate
1- The hopper air pressure is high
2- The powder quantity is more than 3/4th of hopper capacity
3- Recycle to virgin powder ratio is more than recommended
1-1- Reduce the hopper inlet air pressure
2-1- Reduce powder quantity to 3/4th of the hopper capacity
3-1- Add virgin powder to hopper and always limit reclaimed powder up to 20%
1- Inappropriate hose material
2- Moisture or oil in compressed air
3- The air injector components are worn
4- Feed hose is too long or diameter is wrong
5- Air pressure is too low or too high compared to powder quantity
6- Inappropriate hose mounting
1-1- Replace hose with appropriate type (silicone, polyurethane etc.)
2-1- Check air for oil & moisture (Filters and Moisture Traps in the air system)
3-1- Replace nozzle
4-1- Adjust the length and the diameter of the hose appropriate for the powder flow
5-1- Reduce or increase the pressure according to powder quantity
6-1- Mount hoses properly to prevent kinking
1-1- Reduce reclaimed powder and/or increase virgin powder quantity
1-2- Clean the Spray gun regularly and more frequently
1-3- Sift the reclaimed powder before using
1- Unnecessary excessive opening of the paint booth doors
2- Clogged filters inside the paint booth
3- Excessive powder from the spray gun (more than standard)
1-1- Keep the spray booth doors closed
1-2- Switch and adjust inlet and outlet openings based on the size of parts being painted
2-1- Increase Spray booth ventilator suction
2-2- Clean filters and replace them if required
3-1- Reduce the number of guns or decrease the powder from the gun
1- Air velocity is too high causing the powder to disperse
2- Distance between gun and part is inadequate or improper painting technique
3- Powder feed is too high or too low
4- Poor or weak grounding
5- Spraying gun voltage is too low or too high
6- Improper Spray Equipment
7- Powder is too fine
1-1- Decrease the air pressure of spray gun
2-1- Adjust the distance between spraying gun and part (approximately 6 to 8 inches)
3-1- Adjust amount of powder from the spray gun
4-1- Check and secure ground (up to 1 megaohm)
5-1- Adjust voltage to have appropriate coverage in corners and to avoid repelling
6-1- Change spraying nozzle type to a smaller or flat nozzle
7-1- Increase virgin powder or decrease recycling powder
1- High film thickness
2- Powder is wet
3- Powder is contaminated with other materials
4- Part surface is too rough
5- Voltage is too high
6- Changes in the process of powder manufacturing
1-1- Decrease the paint thickness
2-1- Sift and dry the powder and decrease the ambient temperature of the paint system
3-1- Clean the hopper, paint booth and hoses again
4-1- Modify the cleaning and surface preparing procedure of the part
5-1- Reduce voltage
6-1- Consult with powder manufacturer and follow their recommendations
1- Poor charging of powder - The spray gun voltage is unnecessarily high
2- The spray gun and the parts are either too close or too far (gun to part distance is more or less than recommened)
3- Poor or weak earth connection
4- Time of the part in the booth is too short
5- Spray Booth airflow disrupts spraying - Inappropriate air humidity in the spray booth
6- The parts are complex in design or are not hung properly
7- Parts from dry off oven are too hot
8- Powder delivery hose is too long or clogged with powder deposits
9- Foreign particles (Cloth Fibers / Dust etc.) clogging the powder transport system
1-1- Test and adjust spray gun voltage
2-1- Adjust the distance between the gun and the part (standard distance is 6 to 8 inch)
3-1- Check and secure the earth connection
4-1- Reduce line speed, increase powder from the gun or increase the number of the guns in the spray booth
5-1- Test and adjust system configuration and contact spray booth supplier if necessary
6-1- Change the way parts are hung
6-2- Increase / Decrease gun to part distance
6-3- Change gun setting
7-1- Adjust dry off oven temperature or let the parts cool for longer
8-1- Make sure diameter and length of the hoses is proper and that there are no kinks
9-1- Cleaning and maintenance of the transport system should be regular and more frequent
1- Poor grounding
2- Voltage is too low / powder does not charge properly
3- Too much powder output from the gun
4- Powder is too fine or too coarse
5- Conveyor / Racks have too much vibration
1-1- Conveyor / Racks have too much vibration
2-1- Check the gun, cables and electrodes
2-2- Measure gun voltage and make sure the readings match on spraying equipment display
3-1- Reduce powder and / or air flow
4-1- Decrease the amount of the recycled powder (if applicable)
4-2- Contact powder manufacturer to consult about the appropriate powder gun
5-1- Check the system to prevent jerks and shocks to the parts
1- Film thickness is too low or too high
2- Parts do not heat up quickly (Heat up cycle is too slow)
3- Voltage or Air pressure is too high
4- Inappropriate painting technique
5- Contamination with other powders
1-1- Measure film thickness with a thickness gauge and make sure to follow recommendations of the paint manufacturer
2-1- Conduct oven profile (e.g. datapaq) and confirm recommended cure parameters
2-2- May consider preheating the heavy / thick parts
3-1- Adjust air pressure and voltage of the spray gun
4-1- Adjust gun to part distance
4-2- Train painter for gentle passes / strokes of powder
5-1- Clean booth, guns and hoses
5-2- Consult with powder coating manufacturer for incompatibilities
2- Over or under curing
1-1- Clean the coating booth, spraying gun and hoses properly before replacing with new powder
1-2- Avoid using powder coatings from multiple manufacturers in the oven at the same time
2-1- Follow powder coating manufacturer recommendations
2-2- Adjust the oven heat or time parts spend in the oven
3-1- Adjust oven temperature and the time parts spend in the oven
1- Film thickness is too low
2- Different substrates and / or colored materials
3- Faulty spray gun
4- Poor ground and / or Low Voltage
1-1- Follow manufacturers recommendations for film thickness range
2-1- Compare same substrates
2-2- Consult with powder coating manufacturer for similar hiding on all substrates
3-1- Contact spray gun manufacturer
4-1- Check and secure ground and increase voltage
1- Oven temperature is too low
2- The powder is contaminated with smooth powders in the hopper
3- Powder has expired
4- Storage conditions are not favorable
1-1- Adjust and increase the oven temperature per technical data sheet
2-1- Clean the hopper / paint booth and hoses of other powders
3-1- Check the expiration date
4-1- Check storage conditions (Temp and Humidity)
1- Over or under curing
2- Varying film thickness on different areas
3- Improper Oven Exhaust
4- Uneven color due to varying thickness of the parts
5- Paint booth is not properly cleaned of the previous color causing haziness or variation in color
6- Powder is too old or has expired
1-1- Follow Powder Coating manufacturer recommendations
1-2- Adjust the oven heat or time parts spend in the oven
2-1- Apply the powder to the surface evenly and follow manufacturers recommendations
3-1- Check for blockage of the exhaust
3-2- Make sure oven fan is working properly
4-1- Adjust oven temperature and the time parts spend in the oven
5-1- Clean the booth thoroughly before changing or adding new colors
6-1- Use a fresh batch of powder
1- Paint booth is not properly cleaned of the previous color and the contents are incompatible
2- Poor washing that left oil contaminants on the work piece
3- Moisture or oil in compressed air
4- Moisture on the work piece
5- Parts are rusty
6- Surrounding air is contaminated
7- Silicone from the lubricants or sprays
8- The part is porous and outgassing
9- In rough textures, pinholes appear instead of the rolling texture
1-1- Clean the paint booth properly before painting and with every color change
2-1- Test the washing system and make necessary adjustments (contact supplier)
3-1- Check the system for oil and moisture. Replace filters regularly
4-1- Increase dry off oven temperature or the time parts spend in the dry off oven
5-1- Make sure parts do not have rust before painting
5-2- Store parts inside the shop unless painted
5-3- Use mechanical pretreatment like sandblasting or buffing
6-1- Avoid using powder coatings from multiple manufacturers at the same time
6-2- Prevent cross air drafts
7-1- Use silicone free lubricants
8-1- Preheat and outgas's the parts before painting
8-2- Use outgas forgiving products
9-1- Increase film thickness (3.5 - 4.5 mils). Consult powder manufacturer
1- Contaminants from Oven, Booth or Conveyor system
2- Air pressure or voltage too low
3- Feed hose is too long or diameter is wrong
4- Oil and moisture in the compressor air
1-1- Check cleaning procedure and increase cleaning frequency
1-2- Check the paint line for dust contamination and burnout of furnace insulation etc.
3-1- Adjust air pressure and voltage of the spray gun
4-1- Use appropriate length and diameter for the hose
5-1- Check air and oil filters and assure regular replacement
1- Film thickness is too high
2- Undercuring
3- Inadequate or Incompatible cleaning or pretreatment
1-1- Lower the powder or reduce the number of guns to adjust the film thickness to 2.5 to 3.5 for smooth and 3.5 to 4.5 for textured finishes
2-1- Follow manufacturers recommendation. May need to run oven profile to determine suitable baking schedule based on the substrate and parts thickness
3-1- Test the washing system and make necessary adjustments (contact supplier)
1- Inadequate washing and / or poor surface preparation
2- Very High film thickness
3- Parts are rusty
4- Lack of adhesion between 2 coats (primer & topcoat for example)
1-1- Test the washing system and make necessary adjustments (contact supplier)
2-1- Adjust paint thickness based on Manufacturer Standard
3-1- Make sure parts do not have rust before painting
3-2- Store parts inside the shop unless painted
3-3- Use mechanical pretreatment like sandblasting or buffing
4-1- Half bake first coat, apply second coat and then fully bake afterwards
4-2- For heavy parts, preheat the parts and apply both coats back to back and then put in the oven for a final bake
1- Film thickness is too high
2- Substrate temperature is too high (causing a high film build)
3- Powder paint moves to the edges
4- Inappropriate curing conditions (Heat-up rate is too high)
5- Powder falls and accumulates at the bottom of the part
1-1- Decrease the powder from the gun to reduce film thickness
2-1- Increase cooling time between dry off and paint booth, Adjust film thickness as necessary
3-1- Check and secure ground and/or decrease the voltage
4-1- Adjust heat up speed. Check the oven and adjust temperature
5-1- Check and secure proper grounding