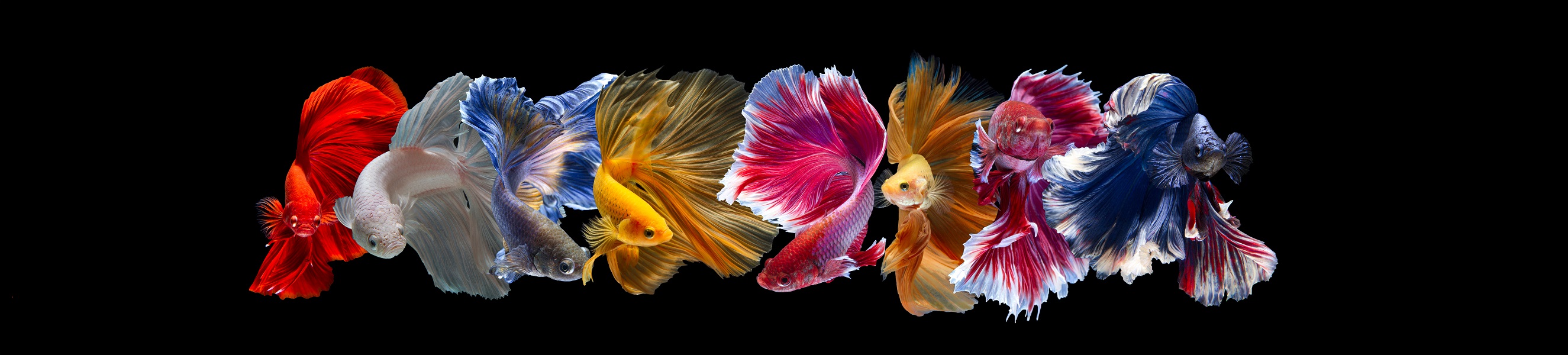
why powder coating
Category: PowderType: Article
9/26/2021
WHY POWDER COATING?
Powder coating is a dry finishing process that has become extremely popular since its introduction in North America over in the 1960s. Representing over 15% of the total industrial finishing market, powder is used on a wide array of products. More and more companies specify powder coatings for a high-quality, durable finish, allowing for maximized production, improved efficiencies, and simplified environmental compliance. Used as functional (protective) and decorative finishes, powder coatings are available in an almost limitless range of colors and textures, and technological advancements have resulted in excellent performance properties.
HOW POWDER COATING WORKS
Powder coatings are based on polymer resin systems, combined with pigments, leveling agents, flow modifiers, and other additives. These ingredients are melt mixed, cooled, and ground into a uniform powder.
A process called electrostatic spray deposition (ESD) is typically used to achieve the application of the powder coating to a metal substrate. This application method uses a spray gun, which applies an electrostatic charge to the powder particles, which are then attracted to the grounded part. After application of the powder coating, the parts enter a curing oven where, with the addition of heat, the coating chemically reacts to produce long molecular chains, resulting in high cross-link density. These molecular chains are very resistant to breakdown. This type of application is the most common method of applying powders. Powder coatings can also be applied to non-metallic substrates such as plastics and medium density fiberboard (MDF).
Sometimes a powder coating is applied during a fluidized bed application. Preheated parts are dipped in a hopper of fluidizing powder and the coating melts, and flows out on the part. Post cure may be needed depending on the mass and temperature of the part and the type of powder used. No matter which application process is utilized, powder coatings are easy to use, environmentally friendly, cost effective, and tough!
In addition to being durable, powder coating is an attractive choice due to environmental advantages. Powder coating is the fastest-growing finishing technology in North America. Its growth can be largely attributed to the following features:
EXCELLENCE OF FINISH
Today’s consumers expect more. They want products that are durable, attractive and long-lasting. When they learn that powder coating protects and preserves like no other, it’s the finish they want from manufacturers.
Powder coatings offer a range of both extreme and decorative performance properties. Compared to other finishes, powder coated surfaces provide greater resistance against chipping, scratching, fading and corrosion. Colour selections are virtually unlimited. High and low gloss, metallic and clear finishes are readily available. Textures can also include various options, such as smooth surfaces, wrinkled or matte finishes and rougher textures designed to hide surface imperfections.
DURABILITY OF POWDER COATING
Powder coating is a high-quality finish found on thousands of products you come in contact with each day. Powder coating protects the roughest, toughest machinery as well as the household items you depend on daily. It provides a more durable finish than liquid paints can offer, while still providing an attractive finish. Powder coated products are more resistant to diminished coating quality as a result of impact, moisture, chemicals, ultraviolet light, and other extreme weather conditions. In turn, this reduces the risk of scratches, chipping, abrasions, corrosion, fading, and other wear issues.
ENVIRONMENTAL PROTECTION
Powder coatings are much more environmentally friendly. While liquid finishes contain solvents that have pollutants, known as volatile organic compounds (VOCs), powder coatings have no solvents and therefore release negligible amounts, if any, VOCs into the atmosphere. Costly waste containment and disposal are not required. Plus, overspray or unused powder is reclaimed and re-used, virtually eliminating the waste commonly found in liquid finishing processes.
EFFICIENCY
With powder coating, there are none of the runs, drips or sags found with liquid finishes. Drying or flash-off time is not required, so the powder coating production lines move more efficiently than standard paint lines. Parts can also be coated using automatic processes that ultimately deliver significantly lower reject rates. With the use of appropriate application equipment, materials and recovery methods, a 95% – 98% powder utilization efficiency is readily achievable.
ECONOMIES OF SCALE
In addition to its efficiency, cost savings are possible because of the simplified line process that powder coating offers. Parts can be racked closer together on the conveyor and pass more quickly through the production line, allowing for lower per unit costs. These production efficiencies are economically beneficial to both the painter and the customer.
ENERGY SAVINGS
The exhaust required in powder coating ovens is lower and therefore helps reduce energy consumption. While ovens that cure solvent-based coatings must heat and exhaust huge volumes of air to protect against potentially explosive fumes, the exhaust volume of a powder coating oven is lower and more manageable. The air can even be recycled back into the plant.