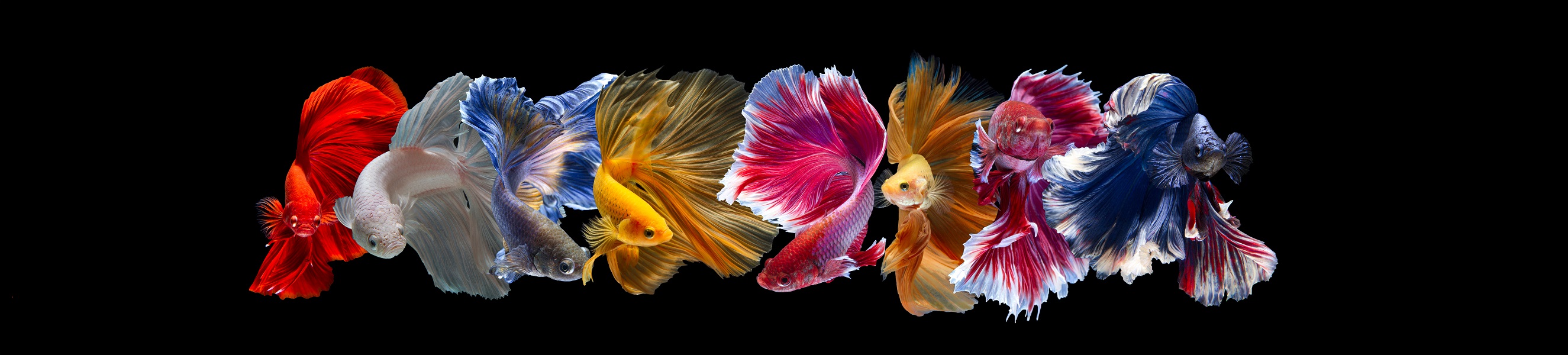
What Is Powder Coating
Category: PowderType: Article
9/10/2021
Electrostatic Powder Coating :
Powder Coating is a manufacturing process called
Electrostatic Spray Deposition (ESD) that employs charged particles to a
workpiece, by electrostatic power and then attracted to the part which creates
a thin and sticky layer on the surface. Powdercoatings are compatible with the
environment because they don’t require solvent and are economical to be
used, which can be recycled and reused many times. Powder coating provides
superior edge coverage and powder coated parts virtually have no drips, runs,
or sags so your part will have a high quality and durable finish.
This is typically used to
achieve the application of the completely dry powder directly to a metal
substrate. The workpiece generally travels down a conveyor belt to the spray
booth with the application method used by a spray gun. After which, the coated
parts enter into an oven baking at 400 degrees Fahrenheit with cure time of
10-30 minutes. During the baking period, the powders melt from the heat and the
coating chemically reacts to make long molecular chains, resulting in high
cross-link density which creates a tough and indissoluble coating.
The powder coating process was
first developed in the 1940s and early 1950s. Initially, organic polymers (or
macromolecules) were “flame-sprayed” in a powder form onto metallic bases. Then
in the early 1950s, a German scientist developed (and then patented) a
fluidized-bed process for Thermosetting Powder Coatings. However, in the 1960s
and early 1970s, two developments combined to build new interest in the powder
coating process. (1) The growing ecology movement and (2) New application
techniques. It was really a combination of these two things that led to the
method’s growth and success. In the 1960s, application by electrostatic spray,
where powder particles are charged and then sprayed onto a grounded material
was then developed.
Powder coatings advantages
1 - Non-toxic and lack of heavy
metal such as lead and cadmium
2 - Very efficient as there is
little waste created in the process
3 - Free of solvents and
harmful vapors resulting in decreasing respiratory diseases and pulmonary
infections
4 - Much more durable than
paint options as the chemical chains and gels together during curing
5 - High safely comparing with
liquid paints regarding fire danger
6 - Easy control and usage and
ready to be used without professional instruction to the painting personnel
7 - Saving time and increasing
production speed resulting in decreasing energy consumption
8 - Because of the recycling
capabilities, it is possible 95% of powder coatings to be used
9 - The high chemical and
physical resistance comparing with liquid paints causes to increase coated
component’s life
10 - This is the best method to
completely customize color and finish
11 - Easy to maintain, no
special solvents or cleaners are required, just soapy water
12 - Does not cause damage to
surfaces, rust or corrosion
13 - The product has a long
shelf life and can be used for many years after which it has been manufactured
14 - The overall quality is
unlike any other paint on the market, since the powder melts and flows together