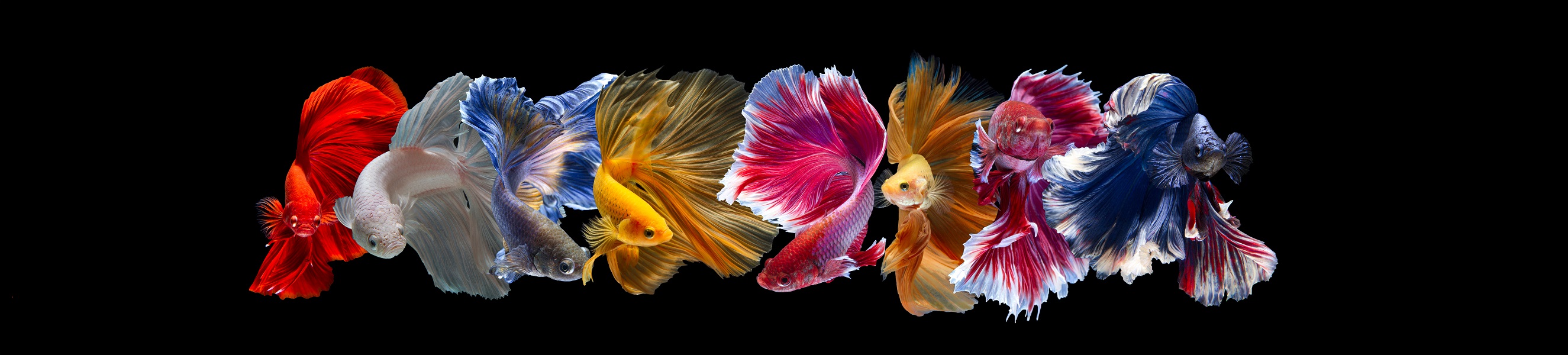
Hiding, Yield & Efficiency
Category: PowderType: Article
9/14/2021
Hiding power, yield and efficiency of powder coatings Calculation
Generally, efficiency is very high in electrostatic powder coatings because of recycling possibility. Hiding power of powder coatings is depended in two important factors; density and particle size.
Hiding power of powder coatings:
1. Smooth colors with thickness 50-70 micron; every one kilogram powder on the smooth surfaces 10-12 M²
2. Sandtex colors with thickness 50-70 micron; every one kilogram powder on the smooth surfaces 8-10 M²
3. Textured colors with thickness 80-100 micron; every one kilogram powder on the smooth surfaces 6-8 M²
4. Hammertone colors with thickness 90-120 micron; every one kilogram powder on the smooth surfaces 6-8 M²
Note: The abovementioned numbers are based on recycling consumption on the smooth surfaces and taken in laboratory calculations and in complicated surfaces with angles definitely will change.
Powder Coating Applying Efficiency
Sometimes a powdercoating is applied during a fluidized bed application. Preheated parts are dipped in a hopper of fluidizing powder and the coating melts, and flows out on the part. When spraying powder by the electrostatic gun, some powders are adhered to the substrate surface and some fall down on the booth ground. Ratio of adhered to powder which fall down is called powder coating efficiency. No matter which application process is utilized, powder coatings are easy to use, environmentally friendly, cost effective, and tough.
Pressure & Air Speed in the Gun
More air speed causes low efficiency and accumulating powder in the corners and angles. Powder particles are directed to the component and
adhered to the component by the help of electrostatic absorption. If the particles movement towards the component is done very fast more than enough, the powder particles hit to the component severely and fall down on the ground. The particles don’t have opportunity to adhere to the component because of the high energy in the air. In general, the less air speed the more adhesion efficiency and less waste.
Gun Distance from Object
In the Tribo powder coating system, material transport is from the velocity at which the powder is liberated from the powder coating gun, that is, from the air flow provided by compressed air. The gun uses a high voltage generator to charge an electrode to a high potential relative to the part. Powders will not stick to the object and fall down if the gun distance is more than recommended. On the other hand if the gun distance is less than recommended, the powders will overcharge because of insufficient voltage and high ampere thus the powders will run away and ejected or causes an orange peel problem. Ideal relative distance for a manual gun varies depending on gun nozzle, object, manual or automatic and application, but usually it is 15cm-20cm from objects experimentally.
Utilizing Suitable Spraying Nozzle
Powder coating spraying gun can be equipped with different various nozzles. Angle nozzles (spraying corners) have high speed transferring powders properties and large width spraying. These kinds of nozzles with more wastes are generally suitable for selective powders such as Metallic, Hammertone and Textured coatings. Round nozzles (spraying round) can be applied as standard in most cases. These kinds of nozzle are offered in different sizes and dimensions. It is recommended to test the nozzle according to their shape and size to get the best result after consulting your gun supplier.
The Negative Effect of Humidity and Heat
Heat and humidity within the working environment can have a significant negative effect on spraying and the powder coating layer quality. Any change in these factors will directly effect on the powder flow in the gun, production efficiency, and the shelf life of cabin filters also powder electrical charge.
More heat will change the powder physical/chemical properties and high humidity will cause agglomeration problems. Supplementary, very dry environments reduce electrostatic charging capabilities and coating layer quality. It is highly recommended environmental relative humidity adjusted between 50–60 and heat around 25°C.
Object and Good Earthing
Good Earthing is one of the important factors in electrostatic spraying equipment. Earthing mat is made by joining the number of rods through copper conductors. It reduced the overall grounding resistance. Such type of system helps in limiting the ground potential. Earthing mat is mostly used in a placed where the large fault current is to be experienced. This maximizes the avoidance of high voltage discharge and the possibility of resultant electrical sparks. Without effectively earthing the spray gun, negative charges will accumulate and powder will then pass through the gun without being charged. The powders will not adhere to the surface. The electrical resistance between the object and good earthing should be always less than 1 Million OHM.
Particle Size & Grading
Particle size and grading should be in a standard limit not very small and not very big. This will directly effect on the layer of the powder and also its waste volume. The powders will move very slow in pistol and pump with very soft and small particle size and cause low movement of electrons and high powder waste amount and charges. However, the larger particle size grading will cause high weight and not adhere to the surface and pouring on the cabin floor and causing problem in farade case with a high voltage.
In over-all, the least costly powder coatings are in big particle size and grading with special heavy weight without standard because of their technical problem. These powders are low in coating with much waste amount, ultimately after final calculation in spite of its low price they will be calculated more expensive than the standard powders with high quality.
Comparison between New Paint & Recycled Paint