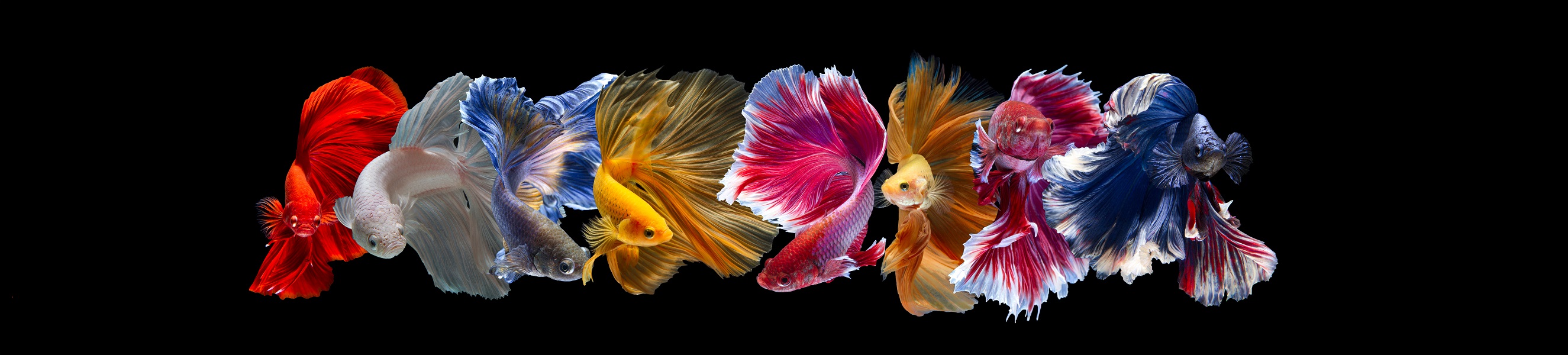
Equipment And Applications Of Spraying Powder Coatings
Category: PowderType: Article
9/26/2021
Differences in nature of powder coats compared to liquid color cause many difference in the methods of spraying and their appliance with each other.
One of the great advantages of powder coating is that we can recycle the wasted powder up to 98%. While in liquid color, these wasted paints cannot be recycled and reused again and this result has a waste of up to 70% of the color used. Equipment and the methods of applying powder coating , which have a great effect (performance of an important role) in this amount of saving wasted powders, are divided into several categories depending on the type of coating and the method of the application process.
Color Type - The powder color is divided into two main groups of Corona and Trioba in terms of the spray system that shows the two types of spray guns with the same name.
1. Corona
Powder coatings charging mechanism is fully depended on the spray gun quality that is used. The most common type of the spray guns is Corona. Most powder coats are designed and manufactured in accordance with this spray gun.
The Corona spray system applies in smooth surface finishes and in the things without any specific complexity or blind angles. Corona spray guns in their simplest shape has a cylinder pipe and the charged electrode at the end. Powder particle passed through the halo of ionized compressed air near the gun and get charged.
Electrode has voltage between 60kw and 100kw in application state that produce a high electric field near the electrode. The powder particle get charged in their passage from this electric field due to negative charge in it to stick to the surface of the plate easily.
One of the limitation of this spray system is lack of absorption of color at the angles with a lot of complexity. We call this situation faraday cage. The colors that are compatible with this system cannot be used efficiently with the Trioba system.
2. Trioba
This system is designed based on charging by abrasion of powder. In this way, the paint powder under pressure from the compressed air passes through a tube with a longer length than the Corona gun. This cylinder is made of special Teflon that contact of the powder with this polymer makes the color positively charged.
Due to the absence of high voltage and uniformity of the electric charge in the particles and the removal of faradays cage, (one of the advantages of this system), coverage at angles and surfaces with complexity and blind spots is applied desirably. The limitation of this system is just the compatibility of few colors to this system, it means that only the colors produced fit to this system can be used in with this kind of spray gun. But, unlike the Coronas color, the colors compatible with Trioba system can be used with the Corona gun system.
In the following we will explain about the ways of applying color, electro static spraying, fluid bed, electro static, etc.
Electro Static Spraying Method
This method is one of the most common applications of spraying powder coating in order to complete the covering process. In this method the technique is as follows;
1. Powder is suspended by the compressed air in the device tank
2. Then transferred to the head of gun by feeding pipes
3. Then by the electrodes embedded in the head of gun, the charged powder particle is applied on the metal surface
The transfer of color between the spray gun and metal surface is the function and combination of electrical energy (electrode of head gun) and mechanical energy (compressor air pressure). Color particle which have electrical charge apply on the metal surface. Magnetic field that produce by the positive charge of color particle and negative charge of metal surface causes the color particles which are absorbed by the metal surface. The compressed air that drives the color particles from the power supply to the gun is also the mechanical force that causes this movement. Non-absorbed particles known as fluidization agent and anti-caking agent powder are referred to color particle that do not absorb on metal for any reason, and spilled on the floor of the cabin or transported by the suction cavity to the cyclone reservoir.
Theoretically, in powder coating, all of these wasted particles can be completely recycled (are completely recyclable.) it means that the powder coating can be used between 95% - 98% and their waste products are between 2% - 5%. While in liquid color their unusable waste product can reach to 70%.
Metal parts should be completely free of any contamination, lipid, corrosion, smoke and dust particles after rinse and prepare the surface and then being exposed to the spray of powder coat. The color is placed in the furnace at specific degree, which depends on the kind of pieces, metal, layer thickness and kind of colors, and processing and curing of powder coat is done.
Continuous flow of powder particles from inside the gun components causes wear and tear of this part of the component, which are mainly made of very compact plastic. This burnout disrupts the flow of powder from the reservoir to the surface. In this method, the color particles are heated up by collision and then melted and they are deposited in irregular pieces in the gun duct and sometimes it has been seen that they accumulated in form of drops at tip of the gun. They call this case; impact melting.
Because of these reasons, injector valve, nozzles and Spray gun tubes need to be controlled and overhauled rapidly. Because they are usually exposed to abrasion and if it needs we should change them. This problem is one of the limitations of the electrostatic spraying method.
Duty of compressed air of compressor is divided into two parts:
1. Liquefy or Fluidize of Powder Coating’s in the Reservoir
In this process we create a quasi-liquid state in the reservoir by combining compressed air into particle and suspending the particles, while eliminating possible humidity is also done in this process. We call this process fluidize.
2. Transfer the Fluidized Particle
This process is done from reservoir to injector and gun and from them to the surface of the pieces (thing) by feeding hoses. Certainly it is necessary that this compressed air should be completely dry and free of any water and oil pollution. Otherwise, it will combine with our powder coat in fluidize stage so this results in contamination of the powder, final coat and some part of our gun. The mixing suitability of the powder and the air compressed is controllable and measurable by the controllers installed on the spray device.
If the pressure of the air in the reservoir reduces, the fluidity of our color will be reduced and then the velocity and density of color will be increased which then causes accumulation of color in hoses and thickness of our color will be higher in some parts of our pieces. However, if our pressure increases, the external powder cloud will be diluted and our cover won’t be completed. In addition, it causes the paint to come out of the reservoir and the cabin, making it to be wasted and polluted the workshop environment.
Fluid Bed or Suspended Particle Chamber
This is the first method and the oldest way of applying powder coating in the 1950s and it is invented simultaneously with production and supply in the market. Despite its simplicity and primacy, it continues to be used as a powder coating process.
In this method, the desired piece is heated under a preheat operation, after the surface preparation enters the reservoir or chamber, where the powder is suspended by the compressed air stream with the desired temperature for curing. The color particles are applying and melting on the surface due to the earth connection and temperature of the surface. Thickness and appliances of powder coating on the pieces relate directly to the concentration of suspended powder, particle size and the temperature of the pieces. If the piece has high thickness and large volume it needs to be reheated again in order to complete the cure after applying and exiting the color out of the chamber.
The main advantages of this process are the simplicity and low volume of the components of this method. In this process we require minimal components:
1. One reservoir or a chamber proportional to the size of the painted parts
2. A grill at the bottom of the chamber to aeration and suspend the particles
3. A tube for feeding the particle to the chamber. A movable valve (gate) is placed to transfer the heated part and then painted part. This collection contains all the components that this method needs
This process doesn’t need a electrostatic spray gun or any weld by mechanical seismicity and cyclone and compared to the electrostatic method, it has lower volume. Meanwhile, due to the enclosure and the preservation of color particles in the suspension cavity, we won’t have the problem of dispersion and pollution of the workshop environment and wasting of color anymore.
The main problem of this method is that it is hard to control the suitable thickness of final covering on the pieces and also control of supplying color to the reservoir and this problem getting bigger in the high circulation and essentially can make challenges for this process during the production in high circulation.
Electrostatic Powder Chamber
This process is more advanced and actually it is the combination of electrostatic spray and suspended powder chamber. In such a way that the mechanism and the structure of this method and its component are similar to the older method, with the exception that by installing the loaded electrodes under the aeration plate of the chamber in the vicinity of its compressed air, such as the corona guns, they are charged electrically and the superconducting pendant powder cloud with an electric charge on a piece attached to the earth connection inside the conduction chamber.
With this practice because our charged particles were applied on the surface, it doesn’t need any preheating before enter the suspended particle chamber but color should be cure in the furnace after coming out of chamber. The main disadvantage of this method is still the problem of supply powder into the reservoir and the way of charging particles but it has less problem like thickness and the quality of coa